3.4. The MULTICONE Junction
3.4.1. Summary
In complement of the interesting properties of the traditional conical junction, the Multicone Junction makes it possible to control the general form of the assembly area of two components, whereas the monoconic junction imposes its geometry, in a restrictive way, at the from the monoconic junction by a cutting in successive truncated zones, the taken zones being laid out in steps to follow closely the desired general form.
In the case of the acetabular implants, the Multicone Junction enabled me to define the thickness of metal independently for each zone in order to satisfy my theoretical principles of resistance to the migration and the swing. The thickness of Polyethylene thus could be maximum for the available volume, thus preserving place for the possible incorporation of ceramics or metal gliding surfaces.
The elasticity of metal supplemented by that of polyethylene brings the implant closer to the ideal isoelasticity. Natural integration in an elastically becoming deformed basin permanently removes the peaks of constraint in certain zones. Lastly, the elasticity of the cup supports its Osseointegration and removes the migration.
3.4.2. Applications of the Multicone Junction
I applied the technology of the Multicone Junction to the assembly of components of the cup implants, in particular the screwed cups Bicon, and to the assembly of the proximal parts to the distal parts of the stems for deep reoperation of the Modular family.
3.4.3. Common properties of the Multicone Junction and the traditional conical junction
The assembly by impacted Conical Junction of two components of an implant present many advantages. It is possible to assemble by this technology components whose materials are of comparable nature or of very different materials. The operation of assembly is always of a great simplicity since after the installation, one or more shocks in the direction of the axis of the cones are enough to obtain the final assembly.
In general, positioning and centering are done naturally and ask neither attention nor adjustment. It is of course preferable to reserve the conical junction to assemblies which work primarily in compression in the direction of the axis.
The application of the conical junction to assemblies requested also in axial traction requires an enough acute angulation to ensure a particularly powerful assembly. If this power is not obtained with a sufficient degree of confidence, an additional mechanical device must be envisaged which prevents a possible separation. If possible, this device must ensure a permanent axial Preconstraint of the junction (example of the assembly by Jonction Multicone of the proximal part and the anchoring part of the prosthesis Modular Plus obtained by a prestressing screw whose head is also conical).
3.4.4. Importance of the surface states.
As already evoked, the components of a conical junction must have a surface quality preventing the axial gliding of conical involved surfaces and be opposed to their separation. Often the two components have extremely different hardnesses and the hardest component receives a surface microstructure intended to encrust itself in corresponding surface of the softest component.
The two current examples are the female ceramics cone encrusting itself on the male microstried cone of Titanium in the assemblies head-neck, and the female microstructured cone of the Titanium cups encrusting itself on the surface with the male cone of the Polyethylene insert.
The angulation of the cones compared to the axis must be given in each case. I point out that there exist conical junctions whose angle is voluntarily more open in order to facilitate a possible disassembling, at the price of risk of Micromovements and wear debris.
3.4.5. Independence of the general forms and the angulations
The angulation of the conical junction is imposed by the nature of the two materials, and cannot be freely selected to adapt to the general shape of the components to assemble. It is this angulation which defines the solidity of the assembly after impaction and its aptitude to support possible efforts in traction.
Two examples show that the angulation imposed by materials makes difficult the application of a monoconic junction, if one wants to satisfy simultaneously other conditions:
1. in the case of a Polyethylene insert in a metal hull, when one wishes the maximum thickness of polyethylene to benefit from his damping properties, the monoconic junction obliges to use an insert of quite lower diameter than the external diameter of the cup. It is the case of all the impacted cups of spherical form whose edge is always very massive and in which the insert because of its loss of thickness loses part of its damping properties.
2. in the case of a cup to which one wishes to give a certain general flexibility, the external form of the cup being more or less close to a spherical form, the monoconic junction is not applicable.
Only the Multicone Junction makes it possible to make the shapes of the components independent from the angulation of the junction.
3.4.6. History of the Multicone Junction
How I imagined the concept of the Multicone Junction?
At the time of my studies of geometrical optics, I had the occasion to take note of work of Augustin Fresnel who, among his multiple work, created the zoned lenses which equip all the lighthouses.
Thanks to his concept of cutting in concentric levels, Fresnel allowed the realization of lenses of very great dimension and very large numerical aperture. If these lenses had been cut from single blocks of glass they would have weighed several tons.
Augustin Fresnel had the idea to preserve the geometry of all optically active surfaces of a large lens by laying out them on concentric circular rings, after the cutting of the large theoretical lens in sections and to remove the thicknesses of glass not having any optical utility. This way, with thin concentric elements, the lens weighed only a hundredth of the same massive lens.
I transposed to the conical junction the philosophy of this cutting in successive sections.
By cutting out in sections a cone of junction of predetermined angulation, we define a series of truncated zones, of decreasing diameters. Among the truncated zones thus defined, we take the elements which will comecloser, by successive steps, of the general shape of the prosthetic component designed to be assembled by conical junction.
This set of truncated levels constitutes what I call â Multicone Junctionâ. The Multicone Junction makes it possible to choose the thickness of Titanium for each level according to the flexibility which we want to give to the cup on this level.
3.4.7. The prestressing of Polyethylene by the Multicone Junction
A conical junction, but more particularly the Multicone Junction, always maintains, after impaction, the male component prestressed inside the female component. I noticed that fixing at large surface of the Polyethylene inserts in the cups is rare among the implants of the market. Often, these inserts, or are ratched in the cup by grooves, or are maintained by circular metal rings.
These fixings, while preventing the insert from arising from the cup, do not provide an absolute immobility. In particular, the cups AlloPro-ZweymĂŒller ( in which I did not participate ), always left play between the cup and the insert. While being of conical appearance, the assembly area of the monoconic cups AlloPro did constitute in no case a reliable junction of impacted conical type. Annular ratching mechanism in the cup prevented the insert from leaving out but did not immobilize it. Moreover, if you shook a cup you could hear the shocks of the insert in the cup.
Micromovements could even involve the production of wear debris of Polyethylene rubbing against a little abrasive interior surface of the cup. More important phenomenon, especially for the small sizes of cups (52 and 55), and for the heads 28, the Polyethylene thickness in periphery of 3 mm might to be crushed. The delamination occurs especially when the prosthetic head is near of the dislocation.
In the vicinity of the maximum contact point the existing play lets Polyethylene move in a viscous way without a tight wall preventing it. By nature, the Polyethylene laminated between two surfaces of the cup and the head tends to adopt a lamellate structure which is detached from the mass, is spread out and made it possible the phenomenon of develop. Crushing and creep are made possible by the absence of Prestressing.
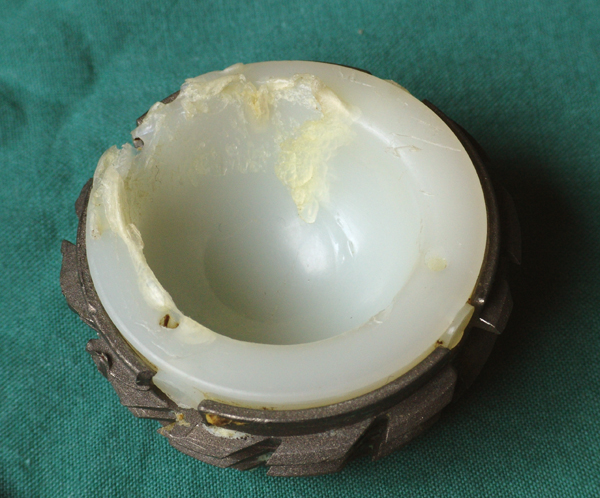
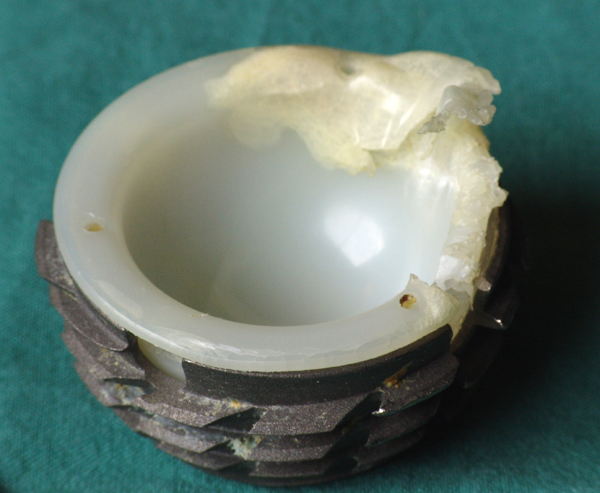
To eliminate these problems, the Polyethylene compressed by the Preconstraint brought by the Multicone Junction resists much more to creep because it does not have place to creep. At the contact point of the head, the Polyethylene even low thickness behaves like a block of Polyethylene of great thickness. The insert contained in a nondilatable Titanium container, in intimate contact and under pressure on all the periphery, cannot become deformed.
3.4.8. Multicone Junction and thickness of the Polyethylene inserts
During meetings of discussion and drafting of the European standards on the orthopedic implants, the thickness of the PE inserts was questioned. Indeed, the Polyethylene inserts, whose wall was too thin and who could move freely inside their cup, could undergo crushings, creeps and delaminations. In contrast, the inserts, connected to the cup by the Multicone Junction guaranteeing to them a permanent prestressing, an intimate contact and without micromovements with the metal wall, did not present these risks. For the inserts with Multicone Junction, it was thus not necessary to apply a constraining regulation on the minimal thickness.
3.4.9. The Multicone Junction of the Modular stems
In the prosthesis for deep reoperation Modular Plus, the Multicone Junction makes it possible to distribute by levels, with a relative continuity, the thinning of the stem during its connection with the proximal part. This way, it does not have an area where the section of the stem decreases too abruptly and weakening the assembly.
The description of the design of the Multicone Junction applied to the assembly of the components of cups, such as for example in the Bicon Plus cup, figure in detail in the French full text of my patent (6.3.3. ).
The reliability of the Multicone Junction applied to cups is remarkable because on the number of cups implanted since 1992 (that I estimate at 500.000), I was not informed of problems or reoperations falling on the Multicone Junction itself. No publication gives a report of dislocation, micromovements, wear debris.
----
My patent âMulticone Junctionâ is since 2009 property of Smith & Nephew.
----